ソリューション
2022.08.5
どのように製造不良率を3%からゼロに改善したのか? TRASAS導入事例 -KTC社内編-
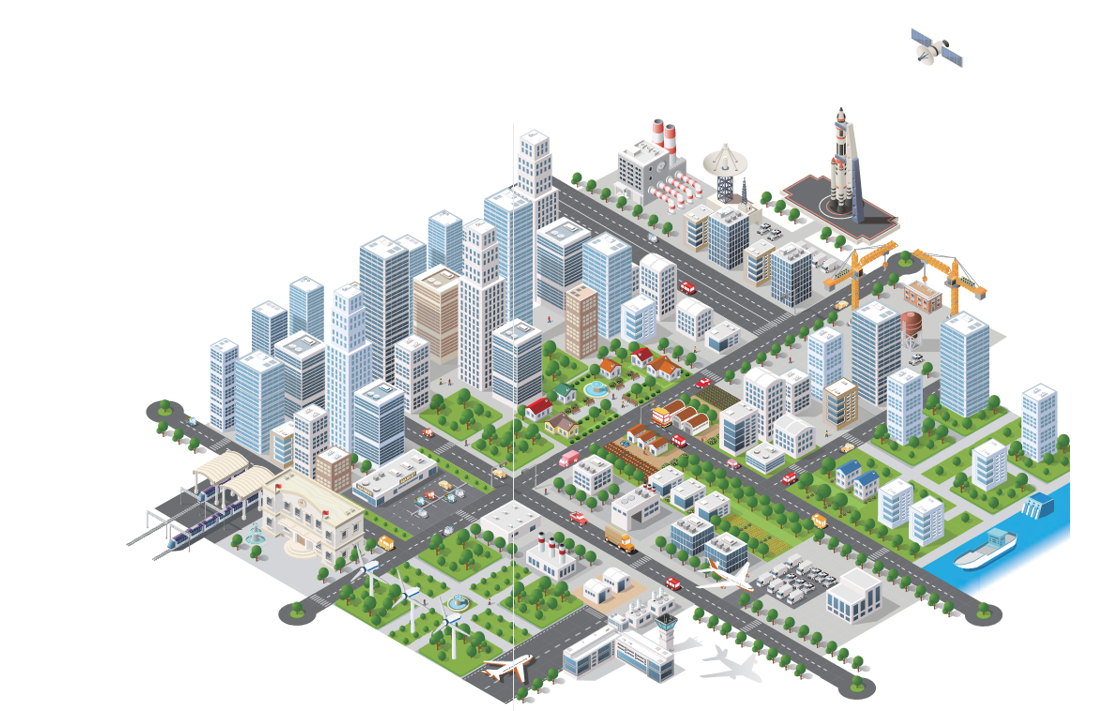
Index
KTCは国内に自社工場を抱える製造メーカーです。1950年創業以降、製造現場における課題に常に取り組んできました。
<<あなたの現場にもありませんか? KTCが抱えていた課題>>
資料ダウンロードやウェビナーアーカイブ視聴、営業へのお問合せについてはページの最後でご案内いたします。ぜひ最後までご覧ください。
これは弊社のラチェットハンドル(以下BR4E)という製品です。
このBR4Eは、マシニングセンターによってクロー穴とギア穴を切削するという製造工程がありました。
当時(約10年以上前)はワークを固定する際に、生産のリードタイム削減のためエアのインパクトレンチを使用していました。エアで仮締めし、本締めはラチェットハンドルで手締めするという工程です。
本締めの加減は熟練作業者の手感覚(勘、コツ、経験)に依存しており、このときは数値によるトルク管理は行っていませんでした。そのため当時のこの工程では加工穴の歪やズレなどの不良が約3%の加工品で発生していました。
そこで、実際にどのくらいのトルクで締められているか調べてみると、目標18N・mに対し、作業者によって20N・m~50N・mのバラつきがあることがわかりました。
どうしても「ゆるいよりはきつめに、しっかりと締めなければならない」という心理があり、強め強めに締めてしまっている実態がありました。
そこで、プレセット型トルクレンチを導入しました。
プレセット型トルクレンチによる仮締め⇒本締め工程は、エアインパクトレンチ使用時よりも作業時間は多少かかりますが、締めすぎを大幅に改善し同時に不良率も大幅に削減。
『勘、コツ、経験』による課題は解決されたかのように思われました。
しかし導入直後からしばらくすると、不良率は徐々に上がりました。
原因を調べると、まだ締め過ぎが発生していることがわかりました。
どうやらプレセット型トルクレンチの使い方が原因であることがわかりました。プレセット型トルクレンチの特性(※1)を理解し作業していたにもかかわらず、作業者には少しでも早く作業がしたい、しっかり締めなければならないという思いが先行し、力を込めた締結が発生。
カッチンと首が折れる感覚があると、なんとなくそれ以降はねじに力がかからないように思っていたという、お話はよく聞くのですが、プレセット型トルクレンチで素早い締結や、二度締めを行うと、正しい設定トルク値での締結はできません。
また、製造現場への要求は日々高まり、生産性をあげつつ、高品質なものづくりをするよう求められ、技術の伝承や社員教育についてもどんどんハードルが上がり、現場の大きな課題になっていました。
>>9.5sq.デジラチェ製品情報(※生産終了モデル)はこちら
>>現行モデルはこちらをご覧ください。https://ktc.jp/dr-new/gew/
プレセット型トルクレンチ使用時の力を込めた素早い締結や、念のための2度締めが多発してしまうという課題を解決するため開発したのが、デジタル式のトルクレンチ『デジラチェ』。ねじに加わっている力をデジタルで測定し、加わった力のピーク値を音や数字でアラートするのが特徴です。
設定したトルク値の力が加わると音と光で作業者に表示するので、経験の差によらず同じトルク値で作業することができます。設定トルクをオーバーすると、エラー音が出るため、締めすぎにも気付くことができます。
この進化は工具大進化(※2)の中でも、技術的大変化点のひとつだとされています。
このデジラチェによって、不良率も1%以下で安定するようになりました。これでKTC的3K『勘(kan)』『コツ(kotsu)』『経験(keiken)』の課題は解決できたように思われました。
(※2)工具大進化とは
しかし最後に若干残ってしまった不良率の不良品を調べたところ、切削穴がずれるものがあり、最後の本締めを忘れていることが原因のようでした。
さらに、そもそも締付自体を忘れており、切削中にワークが外れ、事故につながる恐れのある不良も発生していたことがわかりました。
このような不良を削減するため、紙帳票に作業記録を残していくことになりましたが、記録の手間や手書き後のパソコンへの打ち直しの手間が発生しました。
このような現場の声を受け、「デジラチェ」をバージョンアップする開発が始まりました。
そして2012年「通信式デジタルトルクレンチ『デジラチェ [メモルク]』」を発売。
>>現行モデルはこちらをご覧ください。https://ktc.jp/dr-new/gew/
デジタルでトルクを測定するのはデジラチェと同様ですが、パソコンやタブレットなどの情報機器と通信し、測定記録を自動でパソコンやタブレットに送信できるようになりました。
また情報を受けるPC側のソフトも開発し、エクセルのセルや他社ソフトウェア(例えばi-Reporterのクラスター(※3))など、好きなソフトウェアに必要な情報(作業回数、作業トルク値、作業時間など)を自動で入力可能に。
このメモルクの導入により、作業ごとにペンに持ち替えて紙に記入したり、その紙をあとでエクセルに転記したり……といった手間がなくなりました。
締結忘れを作業記録で確認できるようになり、不良率はついに0%を達成しました。
このように、KTCは自社で起こった課題を解決するため、工具を進化させてまいりました。
ただの締結作業から、トルク管理をすることにより不良率を下げ、トルクの見える化で作業の標準化を果たし、トルクの自動記録で締結忘れをなくしました。
メモルクはKTC社内以外にも、締結作業がある様々な客様の現場で活躍しております。
特に、締結作業によって不良が発生するお客様や、製品が世に出た後に厳しい安全性が問われるお客様、製造部門や整備部門、だけではなく、品質保証部門や開発部門のお客様の下でもご活用いただいております。
今後のウェビナー等でお客様の現場での改善事例も紹介していく予定です。
本日ご紹介したように、デジタルデバイスを使って現場をよりよく変化させることが、現場改善におけるDX(デジタルトランスフォーメーション)です。
DXは『ITの浸透が、人々の生活をあらゆる面でより良い方向に変化させる』という概念です。
このキーワードだけで「ものづくりの現場を改善して」といわれてもなかなか難しいものです。
本日は特に締結作業にフォーカスしてご紹介しましたが、KTCは、締結にかぎらず、特注工具、作業管理、電子帳票化、通信式のデジタル測定器、RFIDによる工具管理まで、さまざまなお客様へのお役立ちをご用意しております。
我々はただ工具やシステムを売るだけではなく、一緒にお困り事を洗い出すところからお手伝いさせていただきます。
なにか変えたいと少しでも思われたら、お気軽にご連絡いただければ幸いでございます。
なぜ工具メーカーKTCが現場のIoT化・作業の見える化を提案するのか? 詳しくご紹介します。
工具大進化Vol01. 安全に対する考え方 ~製品安全への取組みと情報発信~
工具大進化Vol.04 トルクレンチとトルク管理の必要性、 そしてさらなるシステム進化
KTCの歴史と、これから描く未来をご紹介します。